Polystyrene recycling increasing
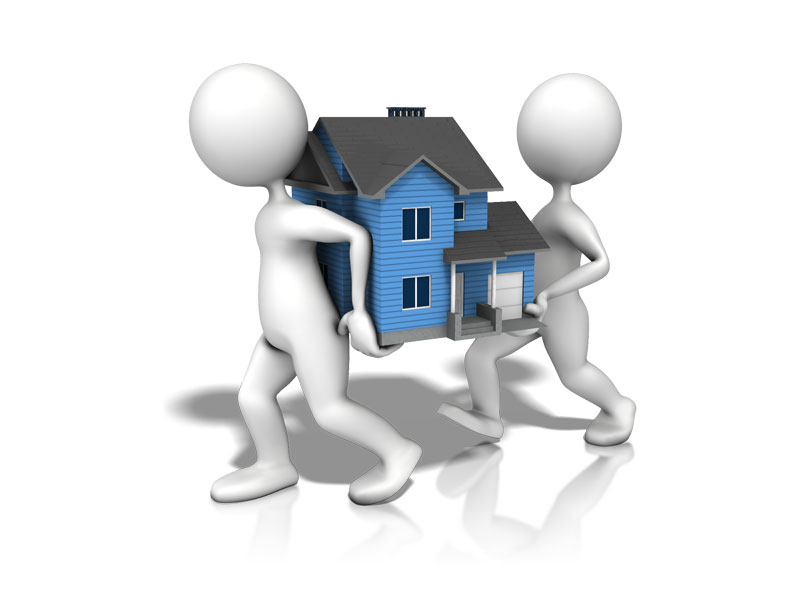
25-01-2021
Read : 518 times
Cape Business News
Source
POLYSTYRENE recycling in South Africa increased by 19 % during 2019, thanks to the tremendous growth in end-markets using post-consumer polystyrene. According to the latest plastics recycling figures for the year ending December 2019 (released earlier by Plastics|SA), South Africa’s plastics conversion rate shrunk by 1.8 % (1,841,745 tons of polymer) compared to the previous year. 337 745 tons of plastics were recycled material into new products during this year.
“South Africa experienced very difficult trading and manufacturing conditions in 2019. Factors such as the economic downturn, ongoing load shedding and the rising cost of electricity, fuel and labour had a particularly negative impact on the local recycling industry. Despite these deterring factors, we are very proud of the fact that we managed to increase our reprocessing of polystyrene to 6,653 tons last year,” says Adri Spangenberg, CEO of the Polystyrene Association of SA (PASA).
Both Expanded (EPS) and High-Impact Polystyrene (HIPS) have traditionally been classified as “plastics that are difficult to recycle”. Because the material is light-weight and often bulky, collection and transportation are challenging and can result in bottlenecks in the supply chain. To address this crucial logistics issue, the PASA began fulfilling the role of a facilitator in 2019. By putting recyclers, collectors and suppliers of polystyrene in contact with each other, the various end-markets that use post-consumer, recycled polystyrene started to enjoy a more consistent supply of recyclate and were able to increase their capacity.
The 39 recyclers of polystyrene reprocessed 3 699 tons of EPS (e.g. meat and fruit trays, hamburger shells, take-away cups and containers) between them. In cubic meters, this equates to 3 237 12 m shipping containers!
The décor market continued to be the largest end-market of EPS packaging materials, with 42 % of all the recycled material going into the manufacturing of items such as picture frames, curtain rods, skirtings and profiles. However, Adri reports that they saw a dramatic increase in the demand for recycled polystyrene used in the building and construction industries, and predicts that this is likely to develop into the biggest end-market during the next reporting period.
“Towards the end of 2019, recyclers such as Envirolite Concrete began expanding their operations around the country. Owing to the fact that they are able to use post-consumer EPS and HIPS in every colour or grade, and thanks to the convenient locations of their factories, we were able to direct more materials to them with shorter lead-times,” Adri says.
These lightweight concrete bricks are made from recycled polystyrene coated with a special cement mixture. Incredibly strong, waterproof, fireproof and offering excellent insulation properties, these bricks are increasingly being recognised by architects, property developers and building contractors as alternative green building materials that are environmentally safe and suitable for a variety of different building applications – ranging from low-cost housing projects to designer homes and even shopping malls.
Interesting facts:
20 kg of recycled polystyrene is used to produce 1 m3 in volume (1000 x 1000 x 1000 mm)
Lightweight cement factories require seven people to produce 10 m3of bricks per day
It only takes 1 day to build 42 m²home, compared to 3 days when using conventional bricks.
Recent News
Here are recent news articles from the Building and Construction Industry.
Have you signed up for your free copy yet?